PPUASB三相分离器 塑料UASB三相分离器 塑料模块三相分离器 厌氧罐三相分离器 IC三相分离器 三相分离器模块 厌氧三相反应器 聚丙烯PP三相分离器
UASB三相分离器焊接技术与化学性能的关系
UASB三相分离器作为污水处理系统的核心设备,其功能是高效分离沼气、污泥和处理后水体。焊接技术作为设备制造的关键环节,直接影响三相分离器的化学性能(如耐腐蚀性、稳定性及使用寿命)。以下从材料选择、焊接工艺、焊后处理等方面,系统分析焊接技术与化学性能的关系。
一、材料选择:焊接技术与化学性能的基础
1. 材料的耐腐蚀性
UASB反应器常处理含酸、碱、盐及有机溶剂的污水,因此三相分离器材料需具备***异的抗腐蚀能力。常用材料包括:
不锈钢(如304、316L):适用于中性或弱碱性环境(pH 6.57.8),316L因含钼元素,耐氯离子腐蚀能力更强。
双相不锈钢或镍基合金:在高温或高含硫污水中,可提升抗应力腐蚀和高温氧化能力。
玻璃钢(FRP)或***种塑料(PVC/PP):适用于低浓度有机废水,但耐温性较差。
焊接技术的影响:
若焊材与母材不匹配(如用普通碳钢焊条焊接不锈钢),焊缝会成为腐蚀薄弱环节。例如,304不锈钢需使用E308/E309焊条,而316L则需专用含钼焊材,以确保焊缝耐腐蚀性。
2. 材料的机械性能
高强度材料(如双相不锈钢)可保证设备在高压工况下的结构稳定性,但其焊接需控制热输入,避免晶间析出相导致脆化。
二、焊接工艺:直接影响化学性能的关键技术
1. 焊接方法的选择
氩弧焊(TIG/MIG):适用于不锈钢和合金材料,通过惰性气体保护焊缝,减少氧化和夹杂,提升耐腐蚀性。
激光焊接:热影响区小,可减少材料变形和热损伤,适用于薄壁结构或高精度部件。
手工电弧焊:成本较低,但易出现气孔、裂纹等缺陷,降低防腐性能。
案例:某污水厂将碳钢三相分离器改为316L不锈钢,并采用氩弧焊替代手工电弧焊,焊缝泄漏率降低90%。
2. 焊接参数控制
电流与电压:过*易导致焊缝过热,形成粗***晶粒,降低耐腐蚀性;过小则可能未焊透,引发渗漏。
焊接速度:过快会导致熔深不足,过慢则增加热输入,加剧材料氧化和应力集中。
保护气体流量:氩气流量不足易造成焊缝氧化,形成贫铬区,加速腐蚀。
3. 预热与焊后处理
预热:对于厚板或高合金材料,预热(100200℃)可减缓冷却速度,避免淬硬组织和裂纹。
焊后抛光与钝化:对焊缝打磨抛光并钝化处理(如酸洗或喷涂防腐涂层),可形成致密氧化膜,增强抗腐蚀能力。
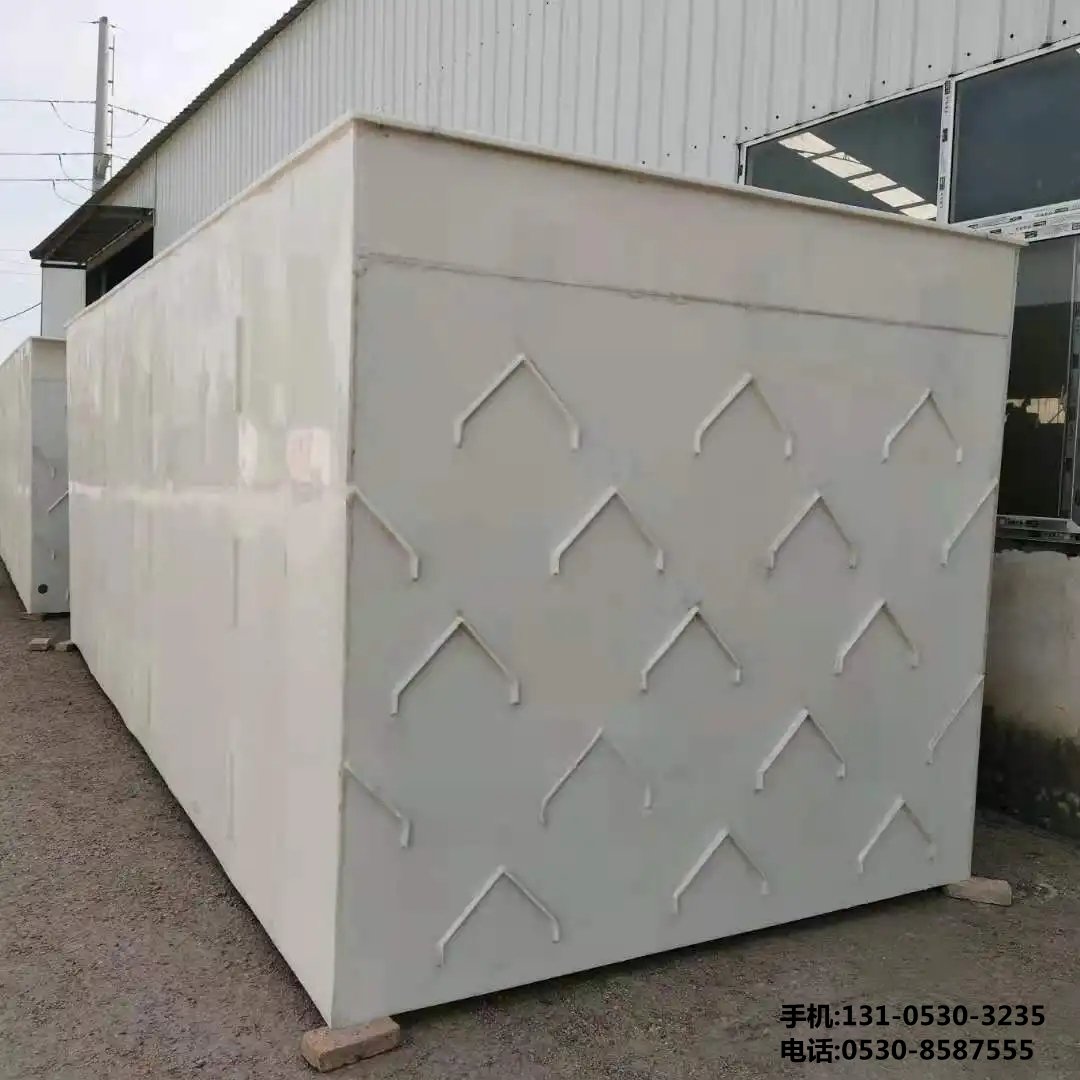
三、焊接缺陷对化学性能的危害
1. 气孔与裂纹
焊缝气孔会破坏材料连续性,成为腐蚀介质的聚集区;裂纹则直接导致应力腐蚀,尤其在含H₂S或Cl⁻的污水中,可能引发快速失效。
2. 热影响区(HAZ)性能下降
焊接高温会导致母材近焊缝区晶粒粗化,降低耐腐蚀性。例如,不锈钢焊接时若未快速冷却,可能析出碳化铬,导致晶界贫铬。
3. 残余应力
焊接产生的残余应力会加速应力腐蚀开裂(SCC),尤其在氯化物环境中。通过锤击处理或退火可部分消除应力。
四、***化焊接技术以提升化学性能
1. 自动化与智能化焊接
采用机器人焊接或激光焊接,可***控制参数,减少人为误差,确保焊缝均匀性和一致性。
2. 焊材创新
使用含钼、氮等元素的高性能焊材,可提升焊缝的抗点蚀和缝隙腐蚀性能。
3. 表面处理与防腐涂层
对焊缝区域进行阳极氧化、喷涂环氧树脂或镀氟塑料,可形成物理隔离层,增强抗化学侵蚀能力。
五、实际应用中的验证与维护
1. 无损检测
通过X射线或超声波检测焊缝内部缺陷,确保无气孔、裂纹等隐患。
2. 定期维护
化学清洗:用酸性或碱性溶液去除结垢(如碳酸钙沉积)。
腐蚀监测:安装传感器实时监测pH、Cl⁻浓度等参数,提前预警腐蚀风险。
结论
UASB三相分离器的化学性能(耐腐蚀性、稳定性)与焊接技术密切相关。通过合理选择材料、***化焊接工艺、严格缺陷控制及焊后处理,可显著提升设备的化学性能,延长使用寿命。未来,随着复合材料和智能焊接技术的发展,三相分离器的性能将更趋高效与可靠。